Head protection at the heart of scientist’s research
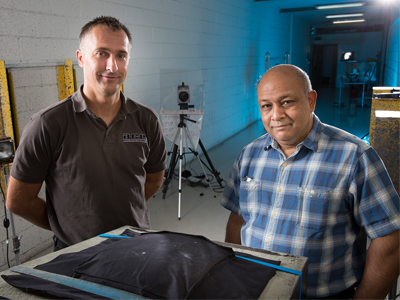
The Defence Science and Technology Group (DST) is responsible for developing individual protection for Australian Defence Force (ADF) personnel, particularly those deployed on operations.
Defence scientist Horace Billon and his team advise clients on how best to maintain their current equipment and guide them on future equipment acquisition.
There are several challenging frontiers in individual protection. One is head protection and, in particular, gaining a deeper understanding of mild traumatic brain injury, which is likely to arise from impact and blast effects.
“What we found is that a lot of the head injury criteria that we use have been taken from the automotive industry,” explains Billon.
“However, the criteria associated with vehicle crashes don’t necessarily cover the whole range of ballistic phenomena, in particular very short duration and very high strain rates.
Need better criteria
“Our challenge is to come up with better criteria which will take a lot of work but is something that would be good for DST to be involved in, potentially through an international collaboration under The Technical Cooperation Program.”
At present, DST researchers most often use the Hybrid III crash test dummy headform for head protection research. This is a hollow headform that contains a suite of accelerometers inside to provide researchers with rotational and translational acceleration information of the head.
The information recorded can be related to the concussive effect of non-penetrating impacts. The same headform also has an instrumented neck that provides researchers with torques and forces at upper and lower neck joints.
“By measuring all these parameters we can relate the head and neck injury criteria to existing medical criteria for injury. That gives us an idea as to whether a particular non-penetrating injury would be survivable, and that information is obviously very valuable to our clients,” says Billon.
“We also have a Canadian ballistic load-sensing headform that was developed with assistance from Defence Research and Development Canada (DRDC). It provides us with information, via a series of load cells, about skull fractures from impacts.
“The heads complement each other in terms of the information we get from them, so for us it’s definitely a case of two heads being better than one.”
One of the DRDC scientists who helped develop the Canadian head, Simon Ouellet, has been working with Billon and colleagues at DST’s Melbourne laboratory this year.
Better picture
In the end, Billon says, it’s all about providing the client with a better picture as to what situations they are faced with and what armour systems are appropriate.
“What I find personally rewarding is the short term problem solving we do. The ADF often need solutions in a hurry,” said Billon.
“In that situation we are under pressure to get quick answers but we always try to give them the best possible solution in the given time frame.
“Sometimes that does mean cutting back on the science ‘frills’ and fast tracking it. In those cases it’s better for us to provide a 70%-80% solution on time, rather than a 100% solution that is too late.”