Mathematics helps composites go beyond
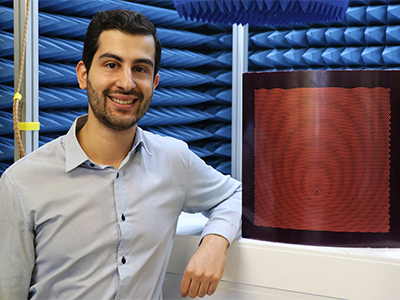
Progress embedding antennas in aircraft surfaces.
After completing two rotations in the Defence Graduate Program, aerospace engineer Joel Patniotis has settled into a position with DSTG in the field of multifunctional composite materials.
After what he describes as an incredible learning curve, Joel is now contributing to cutting edge defence science by designing, simulating, analysing, and ultimately manufacturing new multifunction surfaces that may end up on the aerospace, maritime, and land vehicles of the future.
"Our team has a major research focus on adding extra functionality to composite materials," says Joel. "For example, embedding electronics such as antennas or supercapacitors into composite structures. My current area of research is the development of what are called "artificial impedance surfaces". These are specially designed patterns that can act as antennas. We are able to integrate the patterns into composite materials during the manufacturing process. If you can replace an external antenna of an aircraft with one embedded into its composite surface, then this can reduce the mass and drag of the aircraft, while also making it less prone to damage. Our end goal would be to have these patterns embedded in an aircraft's wing or fuselage."
From idea to instantiation
Joel's work relies on the mathematics and science skills he developed at school and university. "I use both mathematics and science to specify the properties of a new antenna design. Next, I use special software to simulate the antenna on a computer, to assess whether it will work before I construct it."
He is then able to fabricate the sample antenna in the lab. The fabrication process takes several days, requiring thawing of the raw composite materials, inserting the antenna between layers of the composite, and then curing the result in an autoclave. Joel says he's learnt a lot on the job, having no experience in this field when he arrived at DSTG.
Heading towards switchable, 3D multifunctional surfaces
At the moment the team can successfully design and fabricate two-dimensional antennas. But they are aiming much higher, working towards creating three-dimensional antennas that follow the complex curvatures of military platforms. Not only that, these antennas will one day be reconfigurable.
According to Joel, there are several challenges to overcome. The first step is making the antenna structure conformal in three dimensions. The next is making it reconfigurable. The long term goal is for pattern segments to be switched between different values, allowing the radiation pattern to be changed on the fly.
In a recent IEEE journal article, the team shared an exciting achievement, showing that a simple switchable surface with just a binary (on/off) state was possible and effective.
"I'm finding this work really interesting. I'm learning a lot, developing new skills, and can see the end goal. If we can get there, we'll have created some very neat technology that has a potentially significant capability impact for Defence."