Enlisting cutting-edge skills to investigate an aircraft weld failure
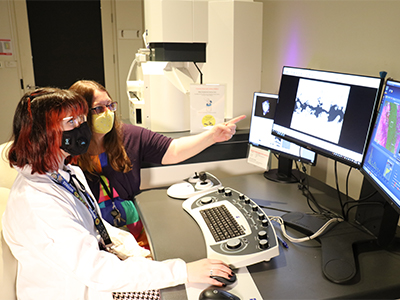
Charli Goodrich is a third-year Bachelor of Science student majoring in chemistry at Swinburne University.
She was one of the many students sharing their placement achievements at the recent DSTEM Defence STEM student conference. ‘I contributed to several projects including the forensic analysis of a weld failure in an afterburner liner,’ says Charli. “That analysis involved assessing the damage to a small section of a repaired afterburner liner using different techniques to investigate the possible causes of the failure.
‘I was fortunate to be placed with supervisors Dr John Thornton and Sonya Slater who are involved in many different projects and, being a real-world office environment, learnt that it is important to be flexible and contribute to the tasks at hand.’
Charli had begun her year-long industry experience placement (IEP) with the analysis of hot corrosion damage (an accelerated oxidation process) to RAAF aircraft gas turbine blades, but that was put on the backburner when the more time-sensitive forensic weld analysis task came along.
Afterburner cracking
So, back to the failed afterburner repair. The process of afterburning temporarily supplements an aircraft’s thrust without the need for a larger engine. The afterburner flame can reach over 1700’C as it burns extra fuel and oxygen to increase the temperature of the exhaust and thus the aircraft velocity, and this high-stress environment often leads to cracking and corrosion.
‘The afterburner sample we received was a small, rectangular section cut from the liner, with a cracked weld repair down the middle of it,’ explains Charli. ‘Our task was to work out why the repair hadn’t lasted. This involved me taking overview images, conducting surface analysis using DSTG’s scanning electron microscope (SEM) including energy-dispersive x-ray spectroscopy. And eventually dissecting the sample to examine cross-sections along the crack.’
The team’s analysis showed significant cracking throughout the weld. According to Charli, the destructive testing was crucial to discovering that the braze had failed. It also helped reveal several other weld non-conformities.
Skills training
During her placement, John and Sonya and colleagues trained Charli in the use of scientific equipment such as the SEM to analyse the topography and composition of samples, as well as forensic photography and optical microscopy, which are important techniques for capturing images of samples before and during destructive analysis. She produced impressive images for both the hot corrosion and forensic projects.
‘In preparing to use the SEM, I learnt how to clamp and dissect samples, set them in resin, polish them and gold-plate them with a sputtering machine to make them conductive (necessary for samples that are to be scanned),” she says. ‘I even had the opportunity to go to the Australian synchrotron with John to analyse samples in the imaging beamline.’
A time slot was booked at the synchrotron for Charli to place a sample of a gas turbine blade in the beamline. ‘The diffraction pattern from the surface allows us to analyse what effect the dirt and corrosion is having on the turbine,’ says John.
Fortunate and grateful
‘I’ve learned things in the last 12 months that I would never have had the opportunity to learn anywhere else, and for that I feel extremely fortunate and grateful,’ Charli reflects
‘As a chemistry major, I had to study engineering and materials science concepts to fully understand my placement tasks. Thankfully I had knowledgeable scientists around me who were always ready to answer my questions and explain new concepts.
‘I thoroughly enjoyed my time as an IEP student here at DSTG. Working in material science has further fostered my interest in inorganic chemistry and I look forward now to exploring this further in the remainder of my degree and in my career.’