Revolutionary stress imaging device takes out National Innovation Award
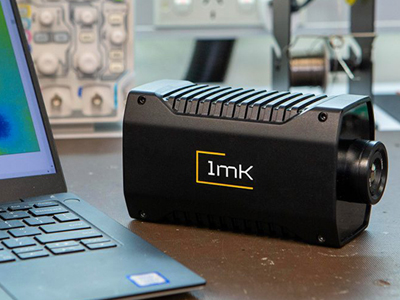
A new robust, lightweight device that is suitable for fitment to aircraft and able to deliver vital stress data in real time has taken out the National and SME Innovation Awards at the Australian International Airshow.
It is the latest development of a technology first developed by Australia's Defence scientists to assess and help extend the life of Australia's F/A 18 Hornets and other Defence aircraft.
The device, not much bigger than a mobile phone, is the second generation of advanced stress imaging systems known as the ITS series (the first generation is known as the LTS-640V) manufactured and distributed by Melbourne-based company 1MILLIKELVIN. The firm was established in 2018 to collaborate with the Defence Science and Technology Group (DSTG) and commercialise this revolutionary capability.
"Our first-generation device was great for imaging stress in a materials testing laboratory," says 1MILLIKELVIN managing director Kheang Khauv. "But the goal was always to take it outside the lab. The second generation is now so light and robust you could have hundreds of these things potentially embedded in the aircraft, while it's flying.
"So you've now got the information in the field as opposed to in the lab. That's what generation two is all about."
The technology underpinning the device – Microbolometer Thermoelastic Evaluation (MiTE) – not only allows engineers to detect metal fatigue, but also to visualise areas of structural vulnerability, and monitor the health of a structure, all at a fraction of the time and cost of traditional techniques.
The technology had been developed by the late 2000s with freeware allowing people to access a cutdown version of the capability in 2013.
Lockheed Martin invited DSTG to demonstrate the technology in 2014. But these versions required separate components – an infrared camera, a digital-analogue converter, a laptop, and a precise calibration process to ensure accurate time synchronisation between camera and load signal.
A commercialisation agreement was signed with DSTG at the Avalon Airshow in 2017 leading to 1MILLIKELVIN's establishment a year later.
The first-generation product developed by the company packaged an industrial grade infrared camera but was still land-based and too big to be practical for use on aircraft in flight. The much smaller and lighter second-generation product is a gamechanger.
The applications go far beyond aerospace with the potential to replace millions of dollars of equipment anywhere where stress testing is safety critical – the mining industry, automotive manufacture, even rollercoasters.
"It's so easy to use, too," says Khauv. "You literally just turn it on, as opposed to needing a science degree to load in the correct calibration files, set the correct integration times, just to get ready.
The 1MILLIKELVIN products were designed and manufactured in Melbourne. They were developed in collaboration with industrial designer Outerspace Design.
"One of the things that we were very strong on, when we first started this project is that this product would be born, bred, and developed in Australia," says Khauv.
The first generation LTS-640V was showcased for the first time in the Singapore Airshow in February 2022 followed by Farnborough in the UK where it was greeted by delighted but sometimes incredulous industry insiders.
"The reaction among people who know existing techniques well is always, 'Oh wow. You can do that?" says Khauv.
Testing the F-35
The first people to have that reaction had been at Lockheed Martin, where the MiTE technology initially earned its stripes in the structural certification testing program for the F35 combat aircraft under the gaze of initially sceptical US engineers.
"That was quite a baptism of fire," says Dr Nik Rajic, from the Defence Science and Technology Group (DSTG), who has worked in lock-step with Khauv to transition this breakthrough. But the technology, that he and his team developed, passed with flying colours.
"We generated real-time stress imagery on a complex bit of structure on the full-scale test airframe – this was the first time something like this had been seen at Lockheed Martin," he says.
The team went on to prove MiTE's worth further in a stress survey on another variant of the F35 at British aerospace company BAE System's facility in Brough, Yorkshire.
Stress - a critical issue
Structural fatigue is a critical factor in aircraft safety. It occurs when an aircraft is subjected to multiple repetitions of the loads caused by manoeuvring, landing, and pressurisation. This creates stresses in the aircraft structure which can eventually result in the cracking of components.
Managing stress fatigue is vital for extending the life of aircraft. DSTG is a world leader in this field thanks to ground-breaking research at its Fishermans Bend laboratories going back to the 1950s. Work there has been vital in assessing and extending the structural life of RAAF aircraft including the Macchi, CT4, Mirage, F-111, PC/9, the F/A-18 Hornet and the P-3 Orion, saving the country millions of dollars and ensuring continuity of defence capabilities.
"What drives this failure is mechanical stress. But for a very long time we didn't have good tools to enable us to visualise or measure those stresses in a structure," says Dr Rajic.
"This technology allows us to do that very rapidly, and in a low-cost way."
Often, the most vulnerable zones of a structure are also geometrically highly complex. "Our technology can visualise the stresses in these complex areas of a structure," says Dr Rajic. "The small rugged infrared camera is installed on the airframe, and in five to 10 minutes of observation we have a high-fidelity full-field visualisation of the stress state."
Every new aircraft type must go through a rigorous structural test.
While scientists, using analysis and data accumulated over decades from testing components to destruction, can predict where stress may become a factor, aviation regulators seldom trust assurances based on analysis alone. They demand that each new airframe design be physically tested to failure before they will certify it as safe-to-fly.
Not only can MiTE expose cracking that results from such testing, it can be used to test stress prediction modelling and help to refine and improve analysis, thus potentially speeding up the structural test program for certification, leading to a shorter development cycle.
"It provides a very powerful tool to test the analysis, and to test it quickly, validating or disproving stress prediction models in a very rigorous way."
MiTE is also much cheaper than current practices, as it uses low-cost, industrial-grade, thermal detectors to take extremely sensitive temperature measurements.
The evolution of testing
Since World War Two, the standard technology to measure stresses and strains in a structure has been the electrical resistance strain gauge. This consists of a piece of electrical resistance wire laid across the area to be tested and circuitry that measures the changes in electrical resistance that occur as the wire stretches and contracts.
But it only measures the stress where the wire is situated. It fails to provide a picture of the stress distribution in a full structure. This is a particular problem with geometrically complex structures such as aircraft.
MiTE, on the other hand, provides an unprecedented view of stresses across the whole structure.
"Aircraft structures tend to fail in and around holes, radius areas, and areas of geometric complexity where it's impractical to bond a standard strain gauge," says Dr Rajic.
"Typically there are no gauges placed in the areas of greatest vulnerability, where the structure is most likely to fail. So traditionally we've not had measurements or observations, the unvarnished truth if you like, about the stress state in the areas we need it most."
MiTE measures stresses using thermoelastic stress analysis. This relies on the fact that, when a solid structure is stressed, it undergoes a temperature change – when it contracts it heats up, and when it expands it cools down.
The technique is not new, having been used for over 50 years. And the theory on which it is based is even older, first being described by William Thompson, Lord Kelvin, in 1853.
This coupling between stress or pressure and temperature is strong in gases, explaining why a bicycle pump heats up, but in solids, the changes are tiny - in technical terms, only about 1000th of a degree for a one megapascal change in stress.
In the past, scientists have been able to get around this using high grade photon infrared detectors which achieve very high sensitivity when cooled to cryogenic temperatures. These devices are fine for laboratories, but impractical for industrial applications.
"These detectors are pretty much the bee's knees in terms of infrared detection sensitivity," says Dr Rajic. "They are used by the military, by firefighters and the police. But the equipment involved is very expensive – typically costing more than $100,000.
"They are they are also bulky devices because they need to accommodate a relatively large cryogenic cooling unit to get the detector down to a temperature of around minus 190 degrees."
The innovation of Dr Rajic's team was to abandon this traditional approach of using photon detectors and turn to more recent advances in infrared detection – specifically small microbolometer cameras.
These cameras use an array of miniature resistors which heat up as infrared energy from the radiating object is focused on them. Such a system only needs temperature stabilisation, not the extreme cooling to minus 190 degrees. And, thanks to signal processing methods developed by DSTG, MiTE typically outperforms traditional detectors in stress sensitivity.
"It's counterintuitive, but we can resolve even smaller temperature variations than the military and tactical applications using expensive cryogenic photon detectors. MiTE is very amenable to stress imaging," says Dr Rajic.