Seeking flight clearance for 3D-printed aerospace components
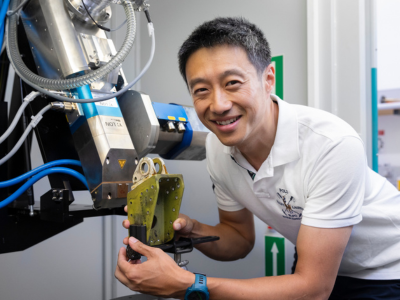
The start of the global pandemic in 2020 was a most challenging time for everyone. Imagine the added stress of starting your Defence science career in Victoria at that time.
Dr Stephen Sun took it all in his stride, and over the last four years has become DSTG's resident subject matter expert in the assessment of the quality, and hence reliability, of aerospace components fabricated using additive manufacturing.
Dr Sun was recently presented with the DSTG Outstanding Early Career Achievement Award. The award acknowledges Dr Sun's significant contributions to a variety of DSTG research projects internally and externally, particularly to the development of additive manufacturing technology and its Defence applications.
One of the current challenges faced by those promoting the use of additively-manufactured aerospace components is the qualification and certification of the components. This challenge can be addressed by combining in-situ monitoring with x-ray computed tomography (μCT or micro-CT). Despite being new to Defence science, Dr Sun put his hand up to lead DSTG's research in this area. It's an area in which he is quite well-versed, having completed a PhD and post-doctoral work at the RMIT Centre for Additive Manufacturing in the area of aerospace component repair using 3D printing.
Big picture, and attention to detail
'My main work now is the research and development of non-destructive inspection techniques for additively-manufactured aerospace components,' explains Dr Sun. 'Let me give you an analogy - you're familiar with the airport luggage screening process, which allows inspectors to find dangerous things before they get onto an aircraft. My work is similar - we put these 3D-printed parts through non-destructive screening processes. This includes taking photos of each layer to identify any potential failure danger.
'Our high-power x-ray CT is used in a way similar to how medical x-rays are used to identify bone cracks. High-power x-rays are needed to penetrate and analyse the dense metal components. We identify potential internal defects and try to link them to mechanical fatigue problems. It's a health check to make sure that there's no danger when we put these components on aircraft.'
Importance of collaboration
With an ability and enthusiasm for developing and fostering relationships, Dr Sun has established partnerships with US Air Force Research Labs and world-leading Spanish 3D printing company Meltio, and three separate research projects with ANU, Monash and RMIT universities.
'Yes, I enjoy collaborating. It means other people do my work. Right?' he says, with a smile. 'Actually, I think with research you have to collaborate. You can't do everything yourself and have a narrow vision. Collaborating has opened my eyes a lot. The universities are brilliant. You meet different people, they have different ideas, and you work towards the same goal.'
According to Dr Sun, the dream is to put high-value, additively-manufactured components on aircrafts. The road block is the complexities of additive manufacturing. 'These 3D-printers are complicated devices. There's a lot of steps involved, and if you get one of these steps wrong, then your printed part may look good on the outside, but may be harbouring harmful defects that will affect the mechanical properties.
'At the moment the aerospace world is just printing door handles or door parts, and other non-critical components. I'm trying to lead the push to print critical parts which are very expensive to manufacture using traditional processes.'
To achieve that, he needs to be certain that the components are reliable and consistent. 'When we give a 3D-printed component to aviation authorities, I really want to be able to say "Yes, this part is trustworthy. We can put it on an aircraft and it's not going to break."'
That's the dream. To get there, Dr Sun and his Defence science colleagues are developing the quality control side of additive manufacturing.
And Dr Sun's plans for the future? 'I love the Obama victory speech catch-phrase "Yes, we can. Yes, we did." That's my motto. I love problem-solving and want to try to solve every problem that's given to me. If you give me a problem, I'll work my butt off to try and solve it.'
Ready to contribute to science and shape the world we live in?
If you're looking for a career in science, technology, engineering or maths, then DSTG is the place for you.
View current vacancies and learn more about the benefits of working at DSTG.