A Layered Approach to Stealthier Undersea Vehicles
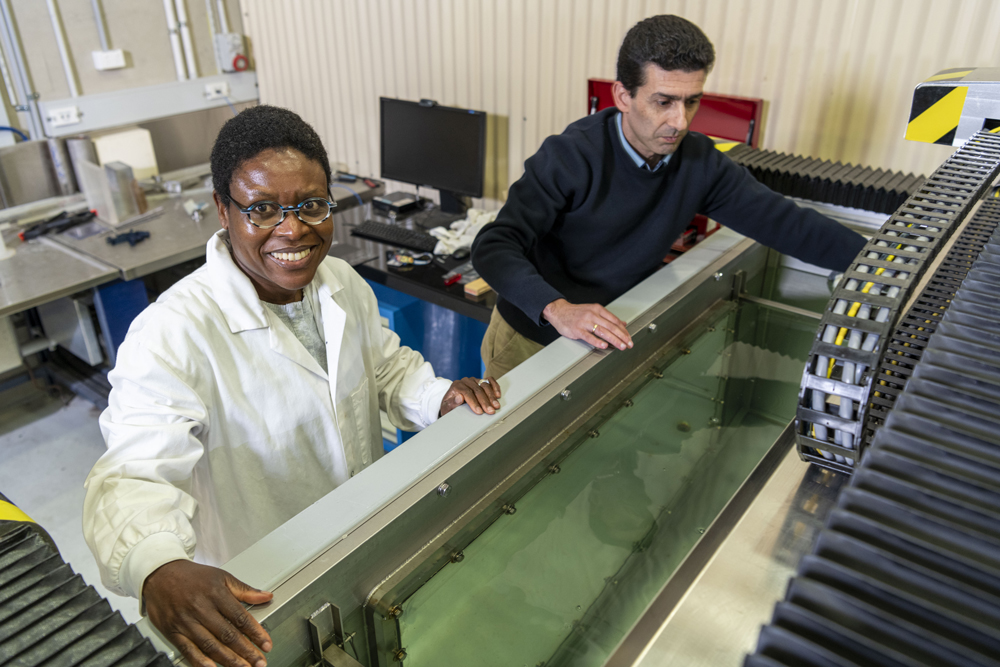
Acoustic materials researcher Dr Gleny Chirima hopes to make our submarines disappear. In her recently-announced Chief Defence Scientist Fellowship, Dr Chirima will investigate an innovative layered viscoelastic coating that could dramatically reduce the signature of undersea vehicles.
Dr Chirima has Masters and PhD qualifications related to polymer materials and composites, and is a member of DSTG's Acoustic Materials research domain which focuses on making undersea vehicles stealthier.
'We study how underwater sound interacts with materials and seek ways to modify materials for controlling sound behaviour in our underwater structures,' says Dr Chirima. The challenging aim is to make platforms invisible to external sensors, while also reducing the acoustic signature emanating from the platforms.
'When sound moves from water to a different material, it will get reflected off that material's surface,' she explains. 'Why? Because of what we call impedance mismatch. Impedance is the resistance of a material to the propagation of sound. If sound is travelling from water to water, it will just go through it like it's invisible. We want to make a multi-layered material, with a first layer matched to the impedance of water so the sound is not reflected. And then we are going to vary the impedances of the subsequent layers gradually until we get to the last layer which matches the impedance of the vessel's hull (steel, for example).
'Having a minimal impedance mismatch between the layers, only a small fraction of the sound gets reflected. Within the multilayer material we'll also have sound absorbing material which will reduce sound emissions from within the vessel.'
Testing teamwork
In addition to the functional aspects of a material, such as the way sound travels through the layers, there are many parameters that need to be considered when designing materials for the highly complex, hostile undersea environment.
For example, the coating is going to be affected by the marine environment and likely to degrade over time, how will performance be impacted?
Working that out is a team effort. While Dr Chirima enjoys the physical testing of potential materials, other team members will be overseeing the modelling of the platform and its environment.
'For my fellowship project we'll try concepts in the lab, and once we understand our material we'll take it further to equipment that mimics the harsh conditions that we experience under the sea. The next step then is to work with an industry partner to test it on a bigger scale.'
Lots of laboratory work ahead
The concept of a matched, multi-layered material has been brewing in the team for a while, and Dr Chirima's fellowship is an opportunity to investigate the game-changing type of material, modify some aspects and verify and understand its potential.
Using raw resin ingredients, Dr Chirima is geared up for a heavy laboratory schedule preparing and casting the viscoelastic material samples in-house at DSTG.
'There are so many parameters that we need to play around with in order to optimise the qualities that we want in the material,' she says. 'Obtaining quality samples through good preparation is crucial, because that determines the quality of results you're going to get at the end of the day.
'The other big challenge I foresee is designing the experimental setup to measure the speed of sound through the materials; we want accurate measurements but the material is designed to stop sound propagation. And a final challenge will be collaborating with an industrial partner to scale up samples to sizes of relevance to real platforms (and then testing those samples).
'I find this work intensely interesting, it keeps me on my toes and makes me look forward to what's coming tomorrow,' says Dr Chirima. 'The ultimate aim would be to cover entire platforms in this material, and if we are successful I'm sure all Defence underwater vessels could benefit from a coating.'