Helicopter Main Rotor Gearbox Planet Gear Fatigue Crack Propagation Test
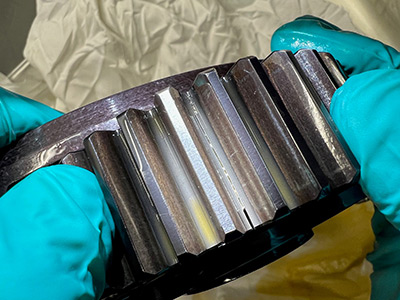
DSTG completed a planet gear fatigue crack propagation test in a retired ADF Kiowa 206B-1 (OH-58) helicopter main rotor gearbox (4-planet version) in January 2022. This test was designed to explore the phenomenon of fatigue cracking in thin-rim helicopter planet gears where the gear body incorporates the outer raceway of the planet gear bearing, and the crack initiates at or near the raceway surface and propagates through the gear body instead of a gear tooth. The crack was initiated from an electric discharge machined (EDM) notch in the planet gear rim and propagated from one side of the gear to the other between two gear teeth. This type of fault is challenging to detect reliably due to the lack of liberated wear debris, and the relatively difficult-to-detect vibration signature. As a result, this can lead to the catastrophic failure of the main rotor gearbox. The test was completed in January 2022 and the latter part of the vibration dataset was initially made available as the HUMS2023 Data Challenge. Results from the Data Challenge were presented at the HUMS2023 conference in February 2023 and are available at HUMS Conference Past Papers.
To reduce the size of the dataset (individual raw data files exceed 84 MB), only the planet-ring hunting-tooth synchronous averages from four vibration channels are available at one torque setting (125%). In this gearbox, the planet-ring hunting-tooth period corresponds to exactly 35 revolutions of the planet carrier, which corresponds to exactly 99 rotations of the planet gear (with respect to the planet carrier). Exactly 12 hunting-tooth periods were averaged to produce the synchronous averages. Both the planet gear and the planet carrier synchronous averages can be derived from the hunting-tooth average (details on how to do this are provided in the notes that come with the dataset).
The original HUMS2023 Data Challenge dataset only incorporated the final 60 load cycles of the test up to the point where the crack propagated all the way through the gear. This was to aid fault detection, as the gearbox was running under more tightly controlled operating conditions (in particular temperature) over this period. There were 526 four-channel planet-ring hunting-tooth average data files in this dataset, with a total size of 6.1 GB.
This second release of the dataset now includes the 34 load cycles immediately prior to the original HUMS2023 dataset, where the operating conditions were slightly more variable. The 287 data files from these extra load cycles add an extra 4 GB, making a total of 10.1 GB.
This release now covers the entire period of the test after the second EDM notch was inserted into the gear rim through to the point where the crack had propagated from this notch to the first notch on the opposite side of the gear. Note that two notches were used because the first (smaller) notch did not initiate a crack during the first 146 load cycles of the test – these load cycles are not part of the dataset.
Various explanatory notes and supplementary files are also included with the dataset. The dataset description document covers the test and data challenge, including particulars such as gear details/mesh frequencies, various diagrams and photos.
A note on the HUMS2023 Dataset
From the results of the HUMS2023 Data Challenge, we observed that some participants have identified notable anomalies in a handful of data files associated with early-stage fault development, e.g. #15, #50, #125, #143 and #150 of the original dataset. See the breakout attachment box for more information and to download the fixed H-SSA files.